Heaters for OEMs Using Plastics and Rubber Processing Equipment
Understanding the Role of Injection Molding Equipment in Plastics and Rubber Processing
Injection molding is a widely used manufacturing process for producing parts by injecting molten material into a mold. This method is indispensable in the plastics and rubber industries and relies heavily on the interaction of various components, particularly heater elements within the injection molding machinery. To understand how injection molding equipment works, especially concerning heater components, it's essential to consider the key components involved: the barrel, nozzle, and molds.
Market Applications: Selecting the Right Process Heater
Injection Molding Equipment
Extruders
Blow Molding Equipment
This page discusses injection molding equipment, specifically. We are actively working on resource web pages dedicated to extruders and blow molding equipment related to injection molding for plastics and rubber processing equipment. Once they are live, we will link them here. Until then, please reach out to us if you have any questions regarding heaters for these applications. We appreciate all inquiries and are happy to help you.
Read this comprehensive guide in its entirety, or conveniently jump to any section by clicking on the links below.
Feature Products - BARRELS
Heaters
Temperature Sensors
Feature Products - NOZZLES
Heaters
Temperature Sensors
Feature Products - MOLDS
Heaters
Temperature Sensors
Injection Molding Equipment
The Role of Heaters in the Barrel
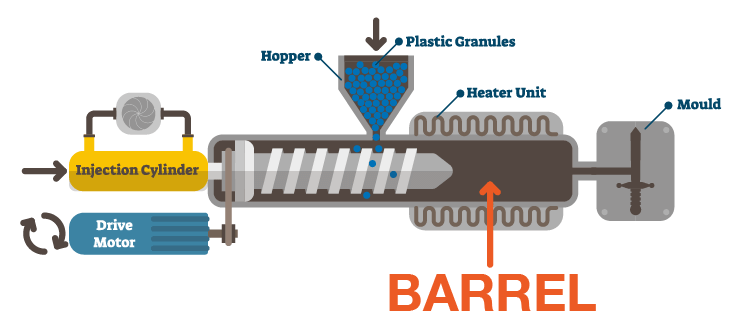
The barrel is a critical component of the injection molding machine where plastic or rubber pellets are fed, heated, and melted before being injected into the mold. It incorporates multiple heating zones, typically using electrical resistance heaters, to maintain a controlled environment as the material reaches its melting point. Proper heating is essential for the optimal flow of molten material, and effective insulation around the barrel helps maintain desired temperatures while minimizing energy loss.
Two primary types of heaters used in injection molding applications are mica band heaters and ceramic band heaters.
Mica Band Heaters
Mica band heaters are frequently used in the barrel of injection molding machines due to their efficient heating properties. These heaters consist of a resistance wire wound around a mica core encased in a metallic sheath. They are designed for moderate temperature applications, operating up to about 900°F (482°C).
Backer Marathon band heaters are computer designed and manufactured to your specifications. Only the highest quality materials are used for optimal performance.
- High temperature oxidation resistant metal sheath.
- Highest grade mica insulation provides excellent electrical insulation at high temperatures and is resistant to moisture.
- Clamping band is low thermal expansion stainless-steel construction, designed to maintain clamping pressure at elevated temperatures.
- Nickel/chromium resistance wire evenly wound for uniform heat distribution and reliable accuracy.
- Standard 10" fiberglass lead wires are UL rated and provide protection up to 850°F.
- Approximately 1/8" thick.
Advantages of Mica Band Heaters:
Quick Heat-Up Times: They heat up rapidly, making them ideal for production environments where quick thermal response is needed.
Cost-Effective: Mica heaters are generally more affordable than ceramic options and effective for many thermoplastic applications.
Ideal for Moderate Temperatures: They are suitable for materials like polyethylene (PE) and polypropylene (PP).
While affordable and efficient, mica band heaters have limitations. They are not as well suited for high-temperature applications, and are best used in controlled environments.
Ceramic Band Heaters
Ceramic band heaters are designed for higher temperature applications and consist of resistance wire coils embedded in a ceramic matrix. Known for their durability, they can operate at temperatures up to 1400°F (760°C) or more, making them ideal for processing engineering plastics like nylon and PEEK.
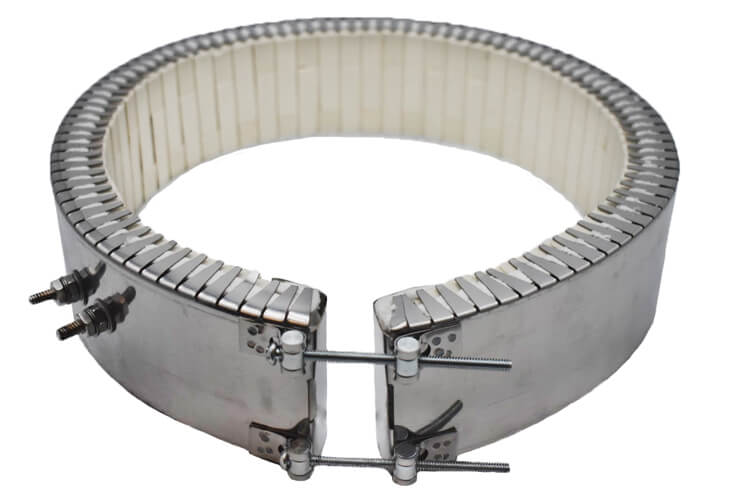
Backer Marathon ceramic band heaters are computer designed and manufactured to your specifications. Only the highest quality materials are used for optimal performance.
- High temperature oxidation resistant stainless-steel sheath.
- Ceramic fiber thermal insulation keeps outer sheath cool and maximizes energy efficiency.
- Clamps are attached directly to the outer sheath providing maximum clamping force.
- Nickel/chromium resistance wire evenly wound for uniform heat distribution and reliable accuracy.
- High-impact, high-temperature ceramic "knuckles" encase the resistance wire for electrical protection and maximum heat transfer.
Advantages of Ceramic Band Heaters:
High-Temperature Capability: Perfect for high-performance materials that require higher melting points.
Energy Efficiency: Good insulating properties lead to better heat retention and less heat loss to the environment.
Durability: They provide a longer lifespan, particularly in high-stress applications and are less prone to thermal cycling damage.
Ceramic band heaters typically take longer to heat up compared to mica heaters and have a higher upfront cost, although their longevity and efficiency may balance this out over time.
The Importance of Nozzle and Die Heaters
Beyond the barrel, heaters in the nozzle and the die play critical roles in ensuring that the molten material retains its ideal temperature during its transition into the mold. Proper heating in these areas prevents solidification and ensures smooth flow, which is crucial for achieving intricate designs and high-quality finishes in molded products.
Efficient heating is vital to the success of injection molding processes, impacting material flow, product quality, and overall production efficiency. Understanding the various heater types available—like mica and ceramic band heaters—allows manufacturers to select the right solutions for their specific applications. By leveraging reliable heating technologies, companies within the plastics and rubber processing industries can optimize their operations, reduce costs, and enhance product output, ultimately leading to greater success in the competitive manufacturing landscape.
In injection molding, the choice between mica and ceramic band heaters largely depends on the specific materials being processed and the operational requirements of the machine. Mica band heaters are great for general-purpose, lower-temperature applications with quick response times, while ceramic band heaters are more suited for high-temperature applications, offering better energy efficiency and durability over longer production runs. For a more detailed discussion, along with a comparison graphic, see this blog.
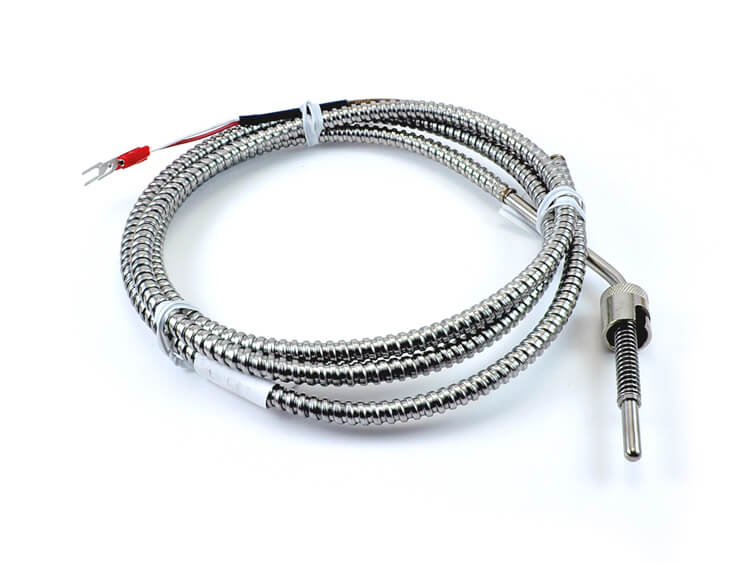
Temperature Sensors
- Adjustable Armor
- Adjustable Stainless-Steel Overbraid
- Fixed Depth
- Shim Style
In injection molding applications, temperature sensors or thermocouples play a critical role in monitoring and controlling the temperatures of various components, such as the barrel, mold, and hot runner systems. Proper temperature management ensures that the plastic or rubber materials are melted, injected, and cooled correctly, leading to high-quality final products. The specific types of temperature sensors—adjustable armor, adjustable stainless-steel overbraid, fixed depth, and shim style thermocouples—serve different functions based on their design and application requirements.
The Role of Thermocouples in Injection Molding
In the injection molding process, maintaining accurate temperature control is critical for ensuring product quality and efficiency. Various thermocouple styles play essential roles in monitoring temperatures throughout the system, helping manufacturers optimize their operations. Below, we explore four key thermocouple types used in injection molding applications, outlining their functions, advantages, and common applications.
Adjustable Armor Thermocouples and Stainless-Steel Overbraid Thermocouples
Role and Function: These two types are employed in general-purpose thermocouples. The adjustable armor thermocouple features a durable, protective metal casing (often stainless steel) that surrounds the thermocouple wire, providing resilience against mechanical stress and high temperatures. This design is ideal for environments where sensors frequently need adjustment or repositioning and offer protection while maintaining exceptional flexibility for routing in tight spaces. The overbraid version also provides a level of protection for the thermocouple wire, while allowing for a bit more movement than the armor version.
Use in both Extrusion and Injection Molding: Commonly used for monitoring barrel temperatures and die heads, these thermocouples can be positioned at various points to ensure precise temperature readings in critical zones: feed, compression, and metering. Their rugged construction protects them from wear and tear, making them suitable for challenging operating conditions. Their flexibility allows for routing through confined areas for accurate mold temperature readings.
Advantages: The adjustable nature allows for easy installation and repositioning as process needs change and the depths of insertion need to be adjusted. They offer high durability, reusability, and reliable temperature monitoring. High flexibility enables installation in awkward or constrained positions; they also provide strong mechanical protection while being easy to adjust during maintenance.
Common Applications: Ideal for monitoring barrel and heater band temperatures, particularly in variable temperature zones.
Fixed Depth Thermocouples
Role and Function: Designed to measure temperature at a precise, predetermined location, fixed depth thermocouples provide accurate and consistent readings due to their consistent installation depth within the mold.
Use in Injection Molding: Often embedded in mold cavities, and can also be used to collect barrel temperatures, these thermocouples help ensure consistent measurements of mold temperature, particularly in critical areas affecting the molding process.
Advantages: They offer high accuracy and repeatability, maintaining stable process control and reliability for long-term monitoring.
Common Applications: Essential for monitoring mold cavity temperatures where exact temperature control is critical, as well as specific points within hot runner systems.
Shim Style Thermocouples
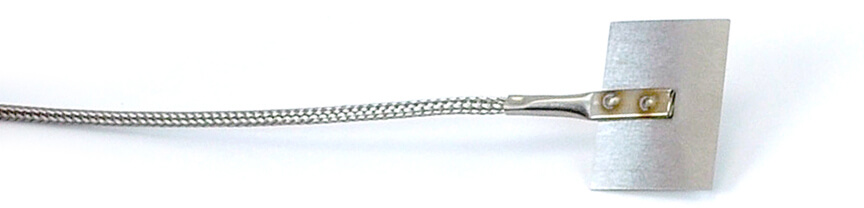
Role and Function: Shim style thermocouples are thin, flat sensors designed for insertion into tight spaces between mold plates or confined areas where traditional probes may not fit. They are also often fit under a heater band itself on the nozzles to determine the temperature at that contact point. Often, shim style thermocouples are used as a short-term workaround until a more permanent thermocouple can be brought to the machine.
Use in Injection Molding: Perfect for measuring mold plate and insert temperatures, these thermocouples allow for accurate readings in areas that do not accommodate larger sensors without altering the mold's operation.
Advantages: Their non-intrusive installation means they can be positioned without modifying existing mold components. They are ideal for measuring surface temperatures in narrow gaps, ensuring accurate functional performance. They do not require drilling into the nozzles or molds.
Common Applications: Frequently used to monitor temperatures in tight spaces or thin sections of the mold, as well as for surface measurements of heating elements on the nozzle or barrels.
Thermocouple Overview
Each thermocouple type serves a unique purpose in maintaining precise temperature control throughout the injection molding process. By employing adjustable armor style, adjustable stainless-steel overbraid, fixed depth, and shim style thermocouples, manufacturers can ensure accurate and reliable temperature readings. This precision is vital for achieving consistent product quality, efficient operation, and reduced cycle times in injection molding applications. By understanding these various thermocouple options, manufacturers can better optimize their processes and enhance their product offerings in the highly competitive landscape of medical and industrial device manufacturing.
Backer Marathon stocks hundreds of different thermocouple models and offers quick turnaround, usually 48 hours or less, on custom designed and manufactured units. We only use the highest-grade materials and offers a variety of sheath materials for any environment or temperature range. All sensors are subject to rigid quality control procedures and a thorough inspection process. Expert engineering assistance is readily available for any order size, large or small. In addition to your sensor needs, we can engineer a complete thermal system for you. Worldwide on-site support is available through one of our many distributors or representatives.
Feature Products: Nozzles
Injection molding is a vital manufacturing process in the plastics and rubber industries, where precision and temperature control are crucial for producing high-quality components. At the heart of this process is the nozzle, which connects the barrel to the mold and serves as the exit point for molten materials. Proper heating of the nozzle is essential to ensure smooth material flow while maintained at optimal temperatures. Various heater types, including mica nozzle heaters and coil heaters, play significant roles in this aspect.
Mica Nozzle Heaters
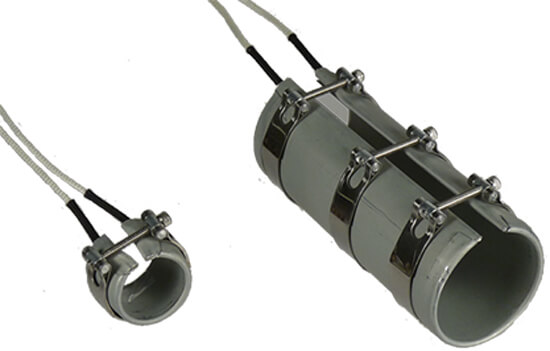
Mica nozzle heaters are widely utilized for heating the nozzle in injection molding applications, constructed with resistance wire wrapped around a mica core and encased in a metal sheath. These heaters are designed for moderate temperature applications, operating up to approximately 900°F (482°C).
Backer Marathon Mica Nozzle Heater Standard Features- Oxidation-resistant metal sheath
- Protective sleeving where leads exit the heater
- Stainless-steel clamping strap with barrel nuts and 6-32 screw
- 10" high-temperature leads with or without SS braid covering
- 1" to 3" diameters available
- 1" to 6" widths available
Also available in low-profile wedgelock construction. These are preferred in areas where the insert cavity diameter is very small, and height off the heater must be minimized.
Advantages of Mica Nozzle Heaters
Cost-Effective: They are generally affordable and effective for many thermoplastics, such as polyethylene (PE) and polypropylene (PP).
Quick Heat-Up Times: Known for their fast-heating capabilities, they facilitate rapid thermal response, reducing downtime in production environments.
Even Heat Distribution: Mica heaters provide consistent heating across the nozzle surface, preventing cold spots that could lead to clogs.
Limitations include lower maximum temperature capability compared to other heater types and reduced durability in harsh conditions. Mica heaters are best suited for applications requiring straightforward heating without extreme performance demands.
Coil Heaters
For more demanding applications, and when a very low profile is required, coil heaters, or high-performance nozzle heaters, are ideal. These heaters consist of resistance wire formed into a coil around a ceramic core, housed in a durable metal sheath, capable of reaching temperatures up to 1200°F (650°C).
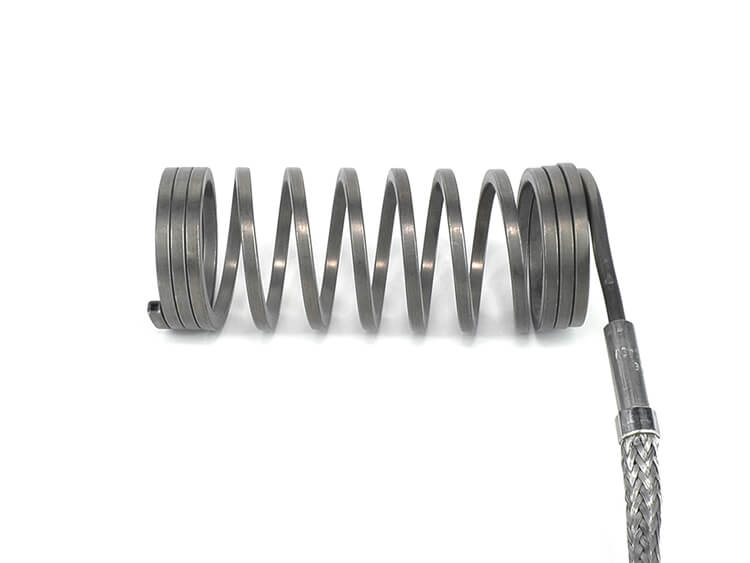
Backer Marathon viper coil heaters feature:
- Flexible Teflon® lead wire
- Stainless-steel sheath
- Nickel/chromium-resistance wire with highly compacted MgO fill
- Available with or without internal thermocouples
(Type J and Type K available for precise temperature control) - 1/8" x 1/8" element cross section
- Seal-welded end
- Ground wire
- 36" stainless-steel braid over leads
- .130 square cross-section is standard
Advantages of Coil Heaters
High-Temperature Capability: Perfect for processing engineering plastics like nylon and PEEK, coil heaters ensure optimal melting temperatures are maintained.
Precise Temperature Control: They provide responsive temperature regulation, essential for preventing material degradation or production defects, such as short shots.
Efficient Heat Transfer: Designed for high watt densities, coil heaters deliver heat effectively in smaller areas, ensuring consistent temperatures while reducing energy consumption.
An integrated Type J or Type K thermocouple can be requested.
However, coil heaters typically come at a slightly higher cost and may have a slower initial heat-up time compared to mica heaters. They are suited for high-performance applications where accurate control and efficiency are critical.
Heater choice is crucial in injection molding processes, directly impacting the quality and consistency of the final products. Mica nozzle heaters are cost-effective solutions for moderate temperature needs, while coil heaters excel in high-performance applications demanding precise control and durability. Understanding these options allows manufacturers to optimize their injection molding processes, ensuring the best results for their specific applications in the dynamic landscape of plastics and rubber manufacturing.
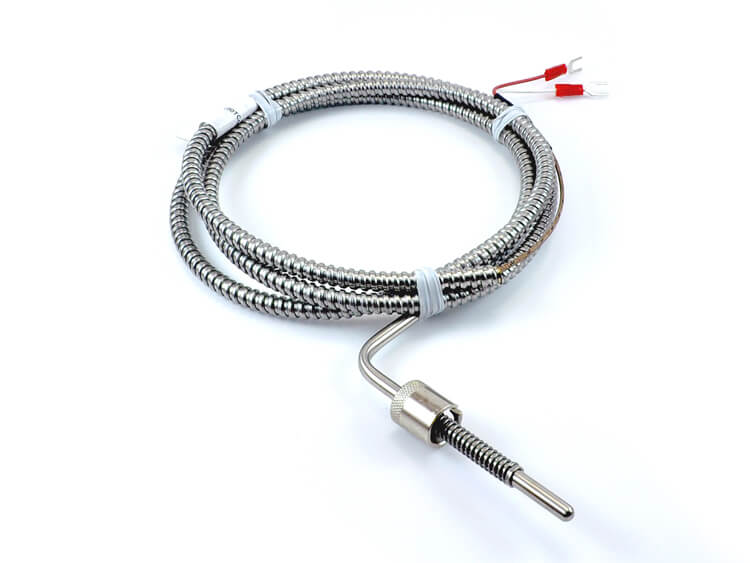
Temperature Sensors
- Shim Style
- Newbury Nozzle
- Nissei Nozzle
- Shallow Nozzle
- Washer Style
- Hose Clamp
Thermocouple Styles and Their Roles in Injection Molding
Temperature monitoring is crucial in injection molding applications to ensure product quality, reduce defects, and optimize cycle times. Thermocouples are widely used to monitor and control temperatures throughout various components of the injection molding system, including the barrel, nozzle, and molds. Different thermocouple styles cater to specific applications and environments within the injection molding process.
Shim Style Thermocouple
Role and Function: The shim style thermocouple is a thin, flat sensor designed for insertion into tight spaces, such as between mold plates or right under a heater band. It specializes in monitoring surface temperatures and can be placed between components without impacting machinery function.
Advantages- Fits into narrow or confined spaces.
- Ideal for non-intrusive temperature monitoring.
Common Applications: Monitoring temperatures in tight areas or measuring surface temperatures of heating elements.
Newbury Nozzle Thermocouple
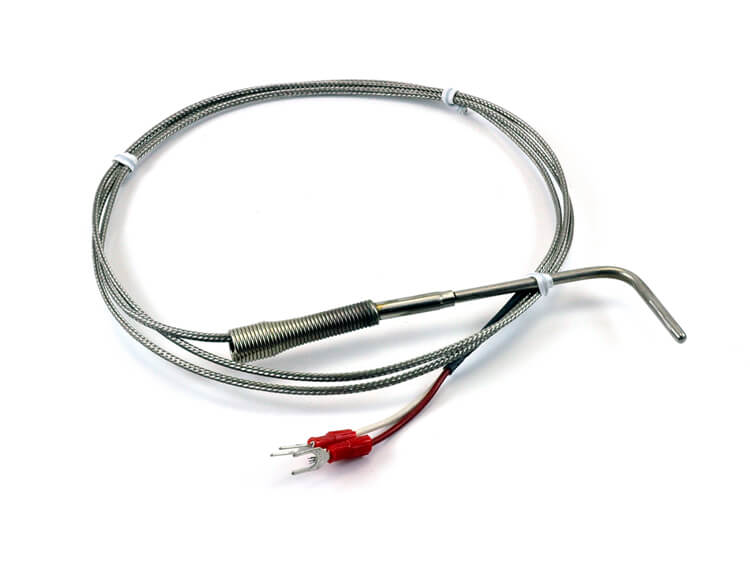
Role and Function: The Newbury nozzle thermocouple is designed specifically for Newbury injection molding machines, providing accurate temperature monitoring at the nozzle to prevent material freezing or degradation.
Advantages- Ensures compatibility and ease of installation with Newbury machines.
- Accurate monitoring of nozzle temperatures.
Common Applications: Used exclusively with Newbury machines for precise nozzle temperature control.
Nissei Nozzle Thermocouple
Role and Function: Similar to the Newbury style, the Nissei nozzle thermocouple is designed for Nissei machines, focusing on high precision to prevent defects in molded products.
Advantages- Provides precise temperature control at the nozzle.
- High compatibility with Nissei machines.
Common Applications: Monitoring nozzle temperatures to maintain consistent material flow within Nissei injection molding systems.
Shallow Nozzle Thermocouple
Role and Function: Designed for low-profile nozzles, this shallow nozzle thermocouple allows monitoring in tight spaces where traditional sensors would not fit.
Advantages- Ideal for low-profile nozzle applications.
- Compact design for precise temperature monitoring.
Common Applications: Used in injection molding machines with shallow nozzles to monitor and control the temperature effectively.
Washer Style Thermocouple
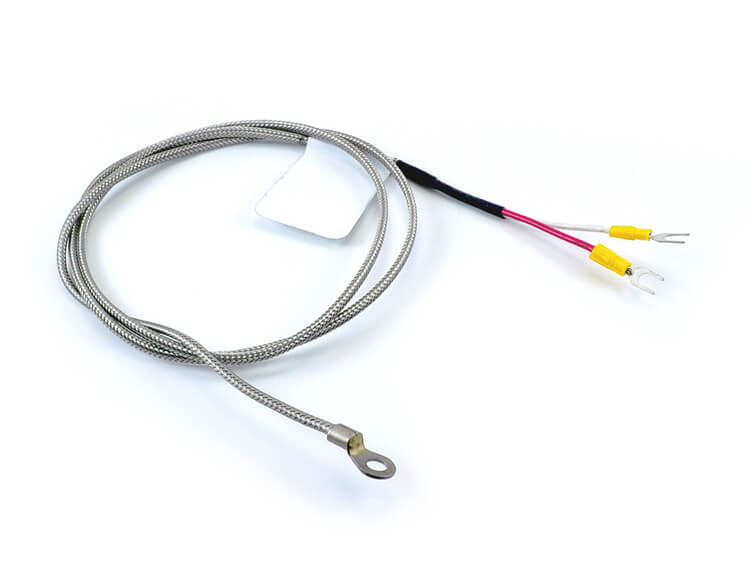
Role and Function: With a washer-like design, this thermocouple is mounted where temperature measurement coincides with mechanical fastening, such as under bolts and screws.
Advantages- Non-intrusive installation at fastening points.
- Monitors temperature effectively at junctions.
Common Applications: Employed in areas where temperature must be measured at the intersection between mechanical parts, such as between the nozzle and heater band.
Hose Clamp Thermocouple
Role and Function: This hose clamp thermocouple design allows the thermocouple to be clamped around cylindrical surfaces like heater bands or nozzles, providing an accessible way to monitor surface temperatures.
Advantages- Easy to install and remove, suitable for frequent repositioning.
- Versatile use on a wide range of cylindrical surfaces and sizes.
Common Applications: Clamped around nozzles, heater bands, or barrels for temperature monitoring, especially where rapid maintenance is necessary.
Each of these thermocouple styles plays a unique role in maintaining precise temperature control throughout the injection molding process. Accurate temperature monitoring is essential for ensuring optimal material flow, preventing defects, and maintaining product quality. By choosing the appropriate thermocouple for specific applications—whether for tight spaces, machine-specific nozzles, or fastened joints—manufacturers can enhance the efficiency and precision of their injection molding processes. This careful selection ultimately contributes to improved product outcomes and operational success in injection molding applications.
Feature Products: Molds
In injection molding, temperature control is essential for ensuring product quality and optimizing cycle times. Molds are the final destination for the molten plastic or rubber. They are designed to shape the material into the desired final product. The nozzle, serving as the exit point for molten material, plays a crucial role in guiding the flow of plastics and rubber into the mold.
Interaction with Heaters
- Cooling Strategies: Most molds feature cooling channels that utilize water or other fluids to manage temperature. In some situations, molds may also include heating elements to maintain specific temperatures, particularly for thermoplastic elastomers. This interaction between heating components and molds is essential for optimal movement and solidification of materials.
- Temperature Control: Keeping a well-regulated temperature in the mold and the heating elements is crucial for balancing solidification time and product quality. Consistent heating and cooling help prevent warping and ensure dimensional accuracy.
- Heat Transfer: The effectiveness of heaters in maintaining precise temperatures is vital for the heat transfer process. Heaters are typically designed and calibrated to deliver the necessary energy for effective heating or cooling, aligned with the specific materials and requirements of the molding process.
Heater Functions and Applications
To maintain the ideal temperature at the nozzle and throughout the molding process, various heater types are employed, including hotset flexible tubular heaters and coil heaters.
Hotset flexible tubular heaters are designed for heating complex mold surfaces, providing uniform temperature distribution. These heaters can be bent or shaped to fit around irregularly shaped molds, ensuring that materials maintain the correct viscosity during processing. These tubular heaters are often used to heat the manifolds through which the molten flow travels through.
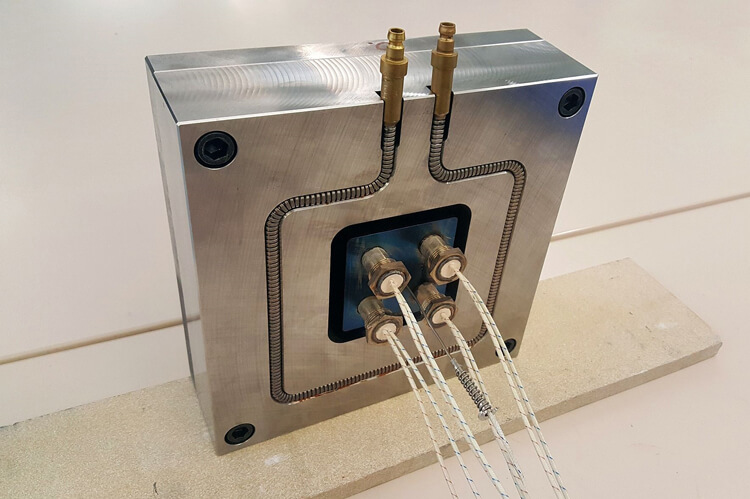
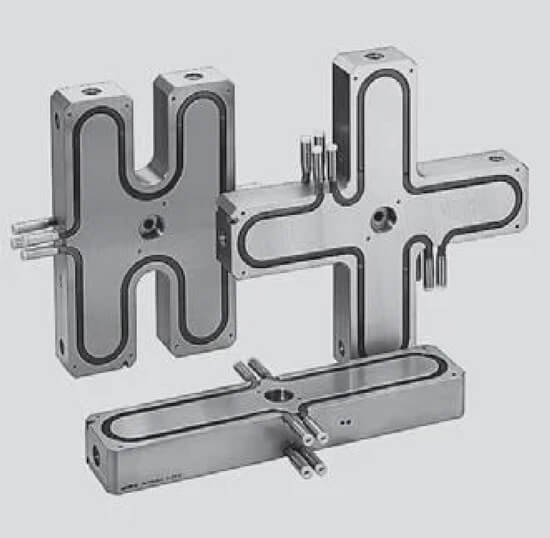
Key advantages include:
- Flexibility: Can be contoured to fit various mold geometries.
- High-Temperature Capability: Suitable for engineering plastics that require elevated processing temperatures.
- Durability: Built to withstand demanding conditions, ensuring long-lasting performance.
Common applications include heating intricate molds that require consistent temperature control to prevent defects, ensuring high-quality part production.
On the other hand, coil heaters are primarily used for nozzle heating and in hot runner systems. They consist of resistance wire wound in a coil form, providing high heat density in compact spaces.
Advantages of Coil Heaters Include:
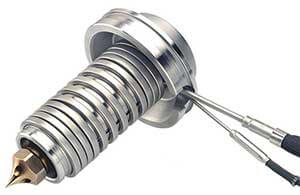
- Precise Temperature Control: They maintain optimal temperatures, preventing material freezing and ensuring smooth flow into the mold.
- Rapid Heat Response: Quick heating and cooling capabilities help reduce cycle times, enhancing production efficiency.
- High Heat Density: Achieves effective heating even in tight and compact areas.
Coil heaters are commonly utilized in multi-cavity molds where consistent temperature management is essential for maintaining uniform material flow. These heaters will often come with built-in thermocouples to monitor the exact temperature and allow the operator to make adjustments right at the point of exit. A specific type of coil heater, a viper coil heater, is used when highly focused heat is required, and a very low profile is imperative. More details on viper coil heaters are provided above on this page; as well, at this link.
Both hotset flexible tubular heaters and coil heaters play vital roles in optimizing the injection molding process. These heaters ensure that the molten plastic or rubber is maintained at the correct temperature, which is crucial for producing high-quality, defect-free parts. Selecting the appropriate heater depends on the specific heating needs of the injection molding process, whether for the molds themselves or for nozzle and hot runner systems.
Temperature Sensors
Mineral insulated (MI) thermocouples are vital for temperature sensing and control in injection molding applications. Their durable and flexible design enables precise temperature measurement in demanding environments, making them well-suited for monitoring critical aspects of the molding process.
Backer Marathon offers a variety of general-purpose mineral insulated thermocouples. MI thermocouples are manufactured at Backer Marathon to address your higher temperature requirements. Since the calibration wire is encased within a metal sheath packed with magnesium oxide the thermocouples can withstand higher temperatures and, depending on the application, will last longer since they are more durable. One excellent feature of mineral insulated thermocouples is faster response time. We stock hundreds of different models and offer quick turnaround, usually 48 hours or less, on custom-designed and manufactured units.
High-Temperature Sensing and Control
MI thermocouples excel in high-temperature sensing, essential for monitoring mold, nozzle, and hot runner temperatures.
Accurate temperature control ensures proper material flow and prevents issues like freezing or burning. Within the injection
barrel, MI thermocouples measure the temperature of molten plastic, maintaining the optimal range for processing—crucial for
preventing defects in molded parts.
Durability in Harsh Environments
These thermocouples are resistant to the high pressures and vibrations generated during injection molding, thanks to the
mineral insulation surrounding the sensing wires. Their metal sheath, typically made of stainless steel or Inconel, provides
corrosion resistance against plastic resins, which helps maintain accuracy over time.
Flexibility in Installation
MI thermocouples can be bent and shaped to fit specific installation needs without damaging the sensor, allowing for precise
placement in tight spaces around nozzles, molds, or runner systems. Their compact design enables rapid response to
temperature changes, essential for maintaining consistent temperatures during the injection process.
Application in Nozzle and Hot Runner Systems
Installed in nozzles, MI thermocouples measure the temperature of the molten plastic as it flows into the mold, preventing
defects like cold slugs. In hot runner systems, they monitor temperatures in the manifold and runner channels to ensure that
the plastic remains fluid.
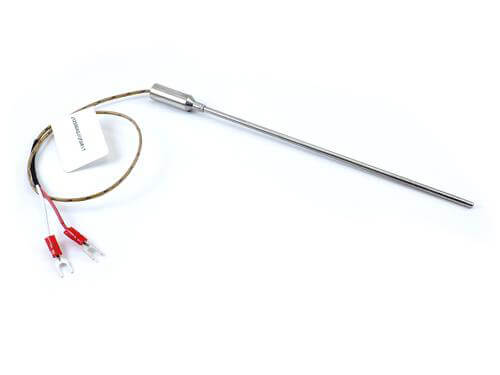
Key Benefits of MI Thermocouples
- Durability: Withstands high pressure, vibrations, and temperatures.
- Corrosion Resistance: Protects against harsh materials.
- Flexible and Customizable: Can be formed for tight space installation.
- Fast Response: Detects temperature changes quickly.
- Longevity: Ensures stable readings in harsh environments.
For a comprehensive view—with specs and options—of mineral insulated thermocouples, look at our product pages here. Mineral insulated thermocouples provide precise and reliable temperature control in injection molding, ensuring consistent product quality and optimizing efficiency in the molding process.
Primary Considerations of Injection Molding OEM Teams
Performance
Heaters and components need to meet the required application levels. When specifying a new heater, the engineering team will
want to relay all critical application details for Backer Marathon's sales engineering team. Application details on the front end
that aren't planned for, can become larger problems longer term. With prior knowledge, the sales team can help anticipate
these potential issues and propose design ideas on the front end.
Key application details will include:
- Temperature Range
- Control System
- Cycling Time, Motion
- Presence of Contamination
- Presence of Moisture
Certifications
Many organizations and process types require certain certifications. Often organizations go through lengthy and involved
process validation processes to ensure repeatability and quality control. You'll want to detail your organizational requirements
to ensure products are manufactured and supplied in compliance with those standards. Backer Marathon is UL, RoHS
Compliant, and ISO9001:2015 and ISO14001:2015.
Energy Efficiency
Just like selecting a furnace for your home HVAC system, or the R Value of insulation, process heaters come in a wide range of
options. To see how they compare, please see our blog that offers insight on how to select a process heater for a ranking of
the different product types among a series of categories. There are some standards, however, in that heaters that are fully
inserted into the process (i.e. cartridge, tubular, and, at times, ceramic strip heaters) will always provide a direct and more
efficient transfer of heat. Any surface heating will lose some percent of the applied energy. You can overcome some of this with
proper industrial insulation, but some heaters, by design, are more efficient than others. The ceramic band heater with its
ceramic fiber tile design is, by nature, one of the most efficient process heaters you can select. It is the gold standard for many
injection molding OEMs when it comes to barrel heating.
(We also created a resource page, Heaters for OEMS in the Plastics Packaging Industry, that might interest you.)
Safety
We've all seen those digital boards that announce, with pride, how many days a facility has operated without recordable
accidents. For companies, it is a point of pride. The goal is to produce quality products in a safe way and have employees return
home to their families each day. There are steps you can take to make your process heaters safe. As a starting point, the key is
selecting the right heater for the job on the front end: correct wattage, correct voltage, and correct style given the application.
Another primary opportunity for safety involves the lead wire connection points—where the power meets the heater. Backer Marathon offers a wide range of terminal boxes, overbraid, armor, and SJO cord. It is also very important to consider adding
grounding wires or grounding posts into your heater, as well. Many organizations require this, but it is always an option to you.
The successful operation of injection molding equipment hinges on the effective interaction between various components, especially the heater systems within the barrels, nozzles, and molds. Heaters enable precise temperature control essential for melting plastics or rubber to ensure that materials flow seamlessly into molds and develop accurately shaped products. Through proper integration of heating strategies within these components, manufacturers can optimize their processes, enhance product quality, and boost overall operational efficiency.
As industries continue to advance, the role of heater components in injection molding machinery will remain pivotal, enabling the successful production of increasingly complex and high-quality plastic and rubber products.
Why Backer Marathon
Our loyal customers have come to know that we anticipate their needs because we actively search for solutions. This is reflected in our advanced quality planning (AQP) lens focused on all that we do. It allows us to be nimble, congruent, and efficient with processes and production. We and our customers benefit from this lean, lessons-learned perspective for each new—or existing—project we successfully execute.
Backer Marathon is part of the Backer North America Group, serving OEMs globally. Being linked with our sister companies under this umbrella provides a wide breadth and depth of resources, expertise, and experience that OEMs benefit from. We collaborate fully with our colleagues, and will source—and manage—the stock and unique custom-heating solutions you need.
We believe in hard work, creative engineering, and excellent customer service. Whether you need one piece or one thousand, Backer Marathon is committed to providing you with exactly what you need when you need it. As we innovate and lead the industry with unparalleled engineering and customer service, we look forward to helping you continue to grow with us.
Let's talk about your next project. Contact us now or call us today at 1 (830) 775-1417. Nosotros hablamos español. We're excited to collaborate with you.